Front line evolution in fluid condition monitoring with CME-AU2000
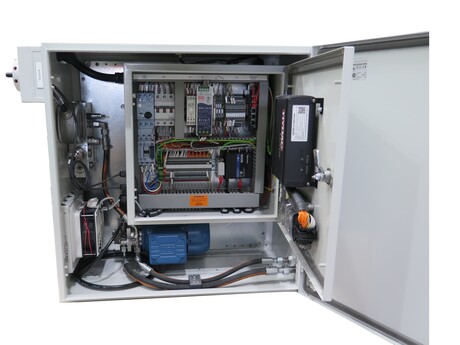
HYDAC’s CM Expert provides a complete fluid condition monitoring package solution for hydraulic and lubrication systems.
The latest version, the CME-AU2000, collects and stores reliable data to offer constant monitoring of fluid health and system integrity; and offers a range of connectivity and accessibility options including expanded I/Os, SCADA integration and SMS/email alarming.
This is achieved through a combination of a range of smart fluid sensors, a central data collection system, Edge computing, and MindSphere© data analytics.
In terms of fluid health parameters, every CME-AU 2000 offers the base capability of monitoring the following parameters:
- Solid particle contamination cleanliness class (ISO 4406)
- Water saturation (%)
- Dielectric constant
- Temperature
System connectivity spans levels
System connectivity options include Level 1, 2 and 3.
Level 1
Level 1, focused on oil analysis, has been designed as a base module to allow integration of condition monitoring easily into the system.
Level 1 includes the following:
- Local accessibility
- Ethernet connectivity
- Wi-Fi monitoring
- On board monitoring and data storage
- Possible integration to SCADA systems
Level 2
Level 2 comes with a central data collection system that monitors itself, automatically interprets data and points out corrective action before problems arise.
Level 2 includes the following:
- All Level 1 features
- Larger IO capacity
- Cloud accessibility
- 3G/4G/Wi-Fi capable (onboard modem/router)
- Local configuration with any device with an internet browser and Wi-Fi
- Data storage via Siemens Mindsphere cloud online portal
- Customisable dashboard
- Active alarming via SMS and emails
Level 3
- Any custom solution which can include all Level 2 features tailored specifically for customer requirements
- Potential to integrate PLC for automated functions, control, and larger IO requirements
HYDAC’s oil condition monitoring Level 1 unit also enables the client to leverage on the Level 2 solution. This means that if a customer has 10 machines in one factory, they don’t need 10 Level 2 units.
The customer can have nine Level 1s, which are cheaper, and bridge them together to one master Level 2 or Level 3 unit depending on the desired outcome.
Level 3 gives a programmable logic controller (PLC) at a local level to allow added control.
For systems requiring condition monitoring of parameters unrelated to fluid health, an Internet of Things (IoT) box is available as a standalone system to monitor and report any data inputs.
For example, HYDAC has applied this technology to monitor driver behaviour on board mining vehicles.
“In effect the CME-AU2000 enables the user to accurately monitor system health in real time and receive early warning signals of potential issues and thus gain the ability to make critically time-sensitive decisions to manually intervene or automate processes to perform maintenance to avoid costly unplanned breakdowns,” concludes HYDAC Engineer Robert Huang.
Writing the Rules for Autonomous Vehicles
Millennials are the consumers of the future and a generation that thinks differently about...
Test electronic designs with Digilent Analog Discovery Pro 3000 Portable High Resolution Mixed Signal Oscilloscopes
The utility of professional benchtop equipment with the flexibility of a portable instrument.
New upgraded pA Metering Module
The product provides users with an easier way to evaluate system performance, and to validate...