IO-Link solutions for the fluid power industry
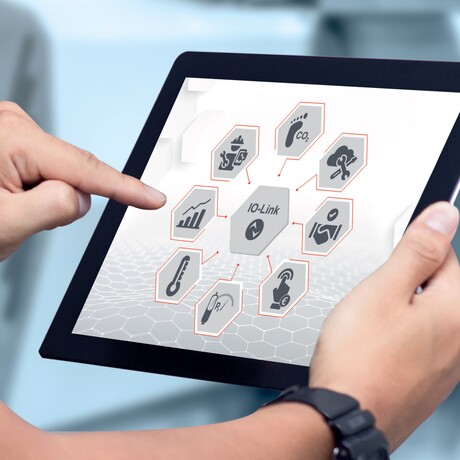
IO-Link is a standardised IO technology that’s used across the world for communication using sensors and actuators. Based on a 3-wire connection, IO-Link communication allows for three types of data to be transmitted, including process data, service data and events.
Simple yet powerful, there are a number of benefits associated with IO-Link communication technology. These benefits include:
- IO-link is universal
IO-Link has been standardised globally, making it universal and compatible. Most I/O-Link devices make use of M12 connectors, which are able to be used without any restrictions when it comes to switching and communication.
- IO-Link is smart
IO-Link technology is smart and boasts high functionality. 2 bytes of process data are available every cycle, and transmission is fast and efficient. Another smart feature is the automatic storage of parameter data for devices. This means when a new device is connected that’s previously been used, its parameters are automatically transferred to save time and hassle.
- IO-Link devices are identifiable
All IO-Link devices have an IO Device Description (IODD). This description file lists information about the manufacturer, functionality and other important details that can be easily read and processed, allowing devices to be easily identified.
The digital IO-Link communication protocol is superior to older analogue systems in that it can transfer both information and process data. This includes:
- Value status (legitimacy of the process data)
- Events (error messages)
- Device information (ID, parameters, diagnosis, and other information)
A major advantage of IO-Link technology is that its data connection is bi-directional. Information can only flow in one direction with typical analogue technology and switch connections, whereas IO-Link gives controls the ability to communicate bi-directionally using a sensor or actuator.
Settings that can only be controlled by manually pushing buttons on conventional pressure switches can now be controlled via IO-Link. This can be done during the start-up stage or even while the operation is in progress.
By remotely carrying out parameterisation work, the commissioning of systems can be done significantly faster, making the whole process more streamlined. This reduces how many error sources occur and minimises the associated costs and machine downtime. This makes IO-Link interfaces an essential component of the IoT, especially in the era of Industry 4.0.
These are some of the IO-Link pressure sensors and transmitters available at HYDAC.
HDA 4000 pressure sensor
Features:
- Compact
- Solid design
- Internal device temperature
- Up to 2000 bar
EDS 824 pressure sensor
Features:
- Mini sensor
- LEDs
- Additional switching output
EDS 3000 pressure sensor
Features:
- Rotatable display
- Additional outlet A/D can be set
HPT 500 differential pressure sensor
Features:
- Filter installation
- Straight forward and robust measurement procedure
- High-precision differential pressure
HPT 1400S pressure transmitter
Features:
- Overload detection / pressure peaks
- Histogram of pressure and temperature outside of permitted usage range
- Device temperature monitoring
- Min/max/average for pressure and temperature
- IO-Link, CANopen, CAN J1939, analogue, switch
Customer benefits:
- Less PLC programming needed thanks to function modules
- Detection of fluid system operation outside of specification
- Simplified troubleshooting in event of damage — short downtimes and service efficiency
- Planned exchange of components across operating time, switching cycles and possibly load profile
- Turnkey solution
Thanks to these functionality enhancements, components with an IO-Link interface are an integral component for digitalisation and the Internet of Things, within the framework of Smart Factory solutions in the fluid power industry.
Sensors for bridge monitoring
To keep bridges going, engineers field data from two fronts: repairs and ongoing maintenance....
People Counting Technology: Integrating ADI EagleEye Adds Intelligence to Your Solutions
ADI EagleEye™ enables a complete end-to-end, edge-based hardware and software technology...
Sensor applications for driving efficiency in electronics production
The laser triangulation sensor has a compact design and is capable of adapting to rapidly...