Three Yamaha YSM20R Mounters Installed at GPC Electronics Maximising Capability and Scalability
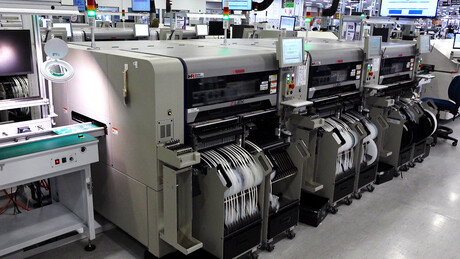
GPC Electronics Pty Ltd is a well-established contract electronics manufacturer based in Jamisontown, NSW, with offices in New Zealand and China. Founded in 1985 by Christopher Janssen, the company ensures high standards across its production processes, from supply chain management to PCB design and expert manufacturing.
Hawker Richardson has been working with GPC Electronics for decades, and with the recent addition of three Yamaha YSM20R mounters, has completed the facility’s fourth production line. Plant Manager Rodney Gibson shares further insights in the full case study.
Rodney — you are the Plant Manager of GPC Electronics. Can you tell us about the company?
GPC is a contract electronics manufacturer. We make products for other companies; we don’t have any product of our own.
We have accreditation to many standards, including Quality – ISO 9001, Medical – ISO 13485, Aerospace and Defence – ISO 9100, and Environmental Systems – ISO 14001. We also have DISP approval and recent accreditation to ISO 27001 – Information Security Management Systems. We have fully implemented SAP as our ERP system across the whole group and utilise an MES system, which allows a great level of traceability for every product.
GPC provides a range of services, including Design for Manufacture and Electronics Manufacturing. Customers come from a range of sectors, including defence, commercial, space, medical, and aerospace. How important is it for GPC to cater for a range of needs, including specialisations such as ruggedised electronics?
GPC offers services to many different market segments in the industry, and each one is unique. We may be building prototypes for new start-ups, and we also build products for larger organisations, such as multinationals, where we build thousands of products.
It is important that GPC has the capability to manage all types of customers. We can help start-ups with their products, develop the processes, and then lock them in. Design for Manufacture and design for test is one part of that. When we do a build for the first time, we can see what processes went right and where there are opportunities for improvement. This allows the process and the design to be fine-tuned for volume production.
You have lots of different brands of equipment at your facility. How well do the Yamaha mounters integrate with those other brands of equipment?
Yamaha surface mount machines fit in line with many other brands of equipment and different processes. From surface mount stencil printers, solder paste inspection machines, board handling equipment, reflow ovens and automatic optical inspection stations. We run the whole cell as one unit, and the Yamahas fit in seamlessly.
GPC now has four lines, and each line has impressive capability with three mounters. How important is it for GPC to offer capability AND scalability?
Capability and scalability are very important. In today’s world, components are getting smaller, and designs are becoming more complex.
We selected the Yamaha YSM20Rs due to the throughput and accuracy of the machines and local support for such critical equipment.
We have now put YSM20Rs into all our facilities. This allows us to quickly transfer product between organisations. We can start a product in Australia or New Zealand and then transfer the product to China. The Yamahas have been integral in making that transfer process very easy.
Having four identical lines in Australia gives us great capacity and flexibility. We can run any product on any line, there are no planning considerations. Our four lines have three modules in each line, which offers a huge feeder account. We build some products which have over 6,000 parts on a board. We can set up those products to run both sides in the one set-up, so lots of flexibility and capacity.
You have made some significant investments over the years that enable GPC to offer impressive capabilities for Electronics Manufacture. How important is it for you to measure each part of the production process to ensure maximum efficiency and productivity?
We verify the performance of major equipment after we have purchased it. When running a surface mount line, we can see the actual machine output and compare that to what is in our ERP system to see whether we are on track with efficiency. We also have automatic optical inspection stations at the end of each line, which look at the quality of the product going through. This information feeds back into a real-time SPC chart so we can verify the quality of the product.
We also ensure that the equipment is utilised correctly. With the surface mount equipment, we went through a quick changeover process, looking to optimise all steps in the process.
One of the outcomes was to invest in more surface mount tables, feeders and software. We could do complete offline setups while machines were running other product. When the changeover occurred, it was quite easy just to move the old tables out, scan new tables to the machines and then we were right to run. We saw huge benefits in that, in the order of 80% reduction in changeovers.
With offices/facilities in Sydney, Christchurch in New Zealand, and Shenzhen in China, how important is it for GPC to draw business from the Australasian market and overseas?
Some businesses like to have manufacturing close to where they are located. They can look at the progress of new products, or there may be special security requirements and, therefore, products must be made in a certain location. GPC can support all these options for customers.
GPC can offer manufacturing from a low labour cost market such as China. The advantage with GPC is that we manage all processes locally for the customer. The customer doesn’t have to deal with China directly. They deal with GPC, and we organise the purchasing, planning, and all aspects of the builds.
We have an International Procurement Office in China and do a lot of our purchasing for the group from there. We can also perform quality audits on products before they ship. Non-compliant product is detected before it is shipped to GPC, improving quality and eliminating delays.
Hawker Richardson has been an SMT equipment supplier to GPC for over a decade. How important is it that your suppliers understand your business and your requirements?
Our suppliers must have a very good knowledge of GPC equipment and processes. If we have breakdowns, they need to make sure we are up and running as soon as possible.
In terms of equipment spares, Hawker Richardson identifies which ones are critical and stores them locally so that if something were to happen, we can be up and running very quickly.
Knowing what we currently do means that they provide good solutions for new equipment straight away rather than going through a process where there’s lots of discussion working out what is best for GPC.
Could you share your overall experience with Hawker Richardson’s service and support?
The overall experience with Hawker Richardson is very positive. We have been working together for a long time, and they have very good knowledge of their product. If something happens to their equipment, we know that they will sort it out quickly.
Hawker Richardson is also willing to help in difficult situations. With the recent purchase of surface mount equipment, we were going to have a long delay due to transport issues at the wharf. Hawker Richardson reduced the delay. We moved the equipment off the boat earlier and transported it across land to get it onsite earlier. The machines were up and running quickly.
Would you recommend Hawker Richardson to anyone else based on your experience?
They are easy to deal with, reliable and always on time. Our experiences have been very good over many years. So, very happy to recommend Hawker Richardson.
Semikron Danfoss and ROHM Semiconductor: partners in power
Semikron Danfoss and ROHM Semiconductor have added ROHM's new 1200V RGA IGBT to its low power...
Comprehensive fluid power training from HYDAC
HYDAC Australia offers a comprehensive range of fluid power training options tailored to meet the...
John Holland employs asset trackers for spoil management
Digital Matter's Nordic nRF9160 SiP-powered Oyster3 and Remora3 form the basis of John...