The clean path to reliable electronic products: Start-to-end PCB cleaning solutions
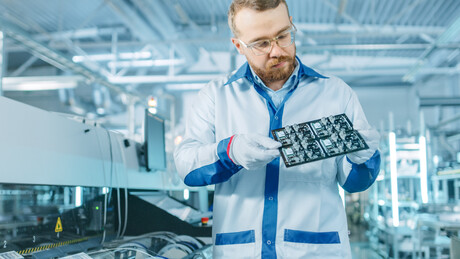
Electronic devices that consumers use every day depend on printed circuit boards (PCBs). Diagnostic or instrument failure can be catastrophic in the medical and aerospace sectors. Many issues can contribute to PCB failure. These include design flaws that result in EMC problems, poor soldering, missing solder paste between pads, and dirty PCBs. Among these issues, PCB cleaning is the most undervalued process during assembly.
Clean PCBs matter
The PCB cleaning process begins at the start of the production line with bare board cleaning and ends with assembled board cleaning. Clean bare boards provide the best possible surface for the next stage of assembly which is component placement. Assembled boards that are clean or defluxed reduce major problems during testing and ensure the functionality of the finished electronic device.
Cleaning is essential to remove ionic contaminants and eliminates the possibility of ECM events such as shorts caused by dendritic growth leakage from ionic residues, current leakage, chemical leakage from components, and changes in impedance. For PCBs undergoing further processing, cleaning is essential for good adhesion of conformal coatings, as non-polar contaminants can compromise their protective qualities.
Challenges around cleaning boards
Today’s sophisticated SMT technology allows for greater flexibility and is suitable for high-density compact designs. Miniature components, multi-layer boards and developments in lead-free solder and no-clean flux add another layer of complexity to the cleanliness required for reliable functionality.
Ensuring thorough drying and rinsing after cleaning is crucial to prevent moisture-related failures and residue accumulation, with multi-layer boards requiring special attention. Additionally, selecting a cleaning agent that effectively removes contaminants without damaging the PCB or components and complies with environmental regulations is critical.
Start-to-End PCB Cleaning Solutions
There are several methods for cleaning PCBs, each suitable for different types of contaminants and manufacturing processes. Start-of-line cleaners include blowers and adhesive rollers, and end-of-line options are solvent, vapour phase and aqueous cleaning.
Start of Line – Bare board cleaners
The best way to start the assembly process is to add an inline PCB cleaning conveyor at the beginning of the line. A bare board cleaner eliminates particle pollution on bare boards to prepare a clean surface for screen printing and better bonding of components to the PCB. This foundational step affects the quality, long-term reliability, and longevity of the finished electronic products.
Bare board cleaners work by blowing contaminants from the PCB or models like the Nutek NTM5000-L In-Line PCB Cleaning Machine use elastomer rollers to remove dust, particles, and glass fibres.
End of line – Assembled board cleaners
The assembly process involves stencil printing, component placement and reflow during which PCBs accumulate no-clean flux residues, grease finger salts, and wave and silicone oils.
Aqueous cleaning solutions are popular with electronic manufacturers as they are eco-friendly and use water or a combination of water and chemicals. Some manufacturers use water-based flux in their paste, which as the name suggests is water soluble — the boards can go through the PCB cleaner with straight water.
Machines like the Aqueous Technologies Trident ZDO are available in zero discharge where chemistries are closed, mixed and re-used and the rinse water is recycled. Closed loop machines mean no waste discharge or need for a waste disposal permit. It is a win for the environment and the manufacturer’s bottom line.
The IMO ECO 2000 is a cost-effective option for small manufacturers offering full recipe control for cleaning, washing, dosing and drying. Able to remove rosin-based, low-residue and water-soluble flux it caters for Euro-card style PCBs with a rack for odd-sized boards. Flux residues are completely removed. The solder joints and components are not attacked and the cleaning agent is completely removed again after the cleaning process.
What cleaning system should you use?
Choosing the best cleaning system depends on the type of flux and solder paste used, the components on the PCB, the required level of cleanliness for conformal coating, and environmental considerations. Properly cleaned PCBs from start to end exhibit enhanced performance, reliability, and longevity, making the cleaning/de-fluxing process an integral part of PCB manufacturing and assembly.
At Hawker Richardson, we have a wealth of experience — over one hundred years and our personalised service includes helping you find the right cleaning product for your manufacturing requirements.
Eliminate Unplanned Downtime: A Smarter Approach to Machine Diagnostics with the HYDAC HMG 4000
The HYDAC HMG 4000 portable data recorder provides a smarter, faster, and more precise approach...
Precision in Design: Specifying Large Handheld Enclosures for Industrial Electronics
When designing handheld electronics, ergonomics play a vital role; purpose-built plastic...
Mouser Electronics: Powering Innovation for Australian Engineers
Mouser Electronics offers cutting-edge components and resources to fuel the next generation of...