How to specify the perfect plastic enclosure for your electronics
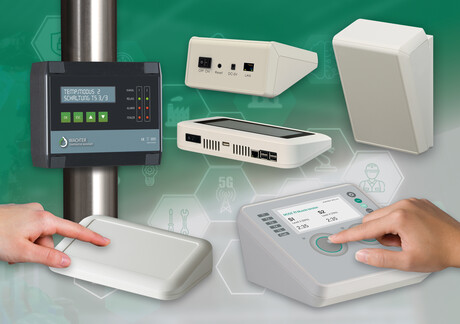
It’s now easier than ever to specify the ideal plastic enclosure for your electronics because there are so many standard models to choose from. But it’s always wise to seek specialist advice — not least because seemingly identical housings may offer very different technical features and benefits.
Start with the obvious questions. What’s your device for? Who will be using it? What will the working environment be like? Will your product be out of harm’s way on an office desk? Or will it be fixed to a wall, machine or bulkhead in a challenging industrial setting?
Getting the ergonomics right is crucial, especially if the device is to be held in the hand or worn on the body. Enclosures that feel awkward or uncomfortable are unlikely to find favour with the end user — especially if the device is in use for extended periods.
“Initial impressions always matter,” said Shane Dwight, Managing Director of ROLEC OKW Australia New Zealand Pty Ltd. “The enclosure is the first thing a user will see and touch, so its aesthetics and ergonomics are critical.”
Many desktop enclosures are designed with a sloping top, making it easier to view a display or operate controls. This also makes these housings perfect for wall-mounted electronics such as access control keypads. A recessed top to protect a membrane keypad or product label is a standard feature on many models, whether they are desktop, wall-mounted, handheld or wearable. Some housings, such as OKW’s desktop/wall-mountable EVOTEC, offer a flat or sloping top as standard. UNITEC, for dual-user applications such as point-of-sale, has two operating faces and a wraparound recess for an all-over product label.
Whether or not the enclosure will be used outdoors will have a bearing on the materials used. Generally, Acrylonitrile Butadiene Styrene (ABS) used to be the default choice for many plastic enclosures, and it remains very popular. ABS is highly durable, has good resistance to heat and many chemicals, and is easy to mould, machine and finish.
But ABS isn’t as tough as polycarbonate, which can withstand much higher impact forces: up to 850 joules/metre compared with 200 j/m for ABS. PC is made up of long chains of carbonate groups linked by strong bonds. This allows energy to be absorbed and distributed across the material. So enclosures such as SOLID-BOX are moulded from a PC+ABS blend. This makes it a credible contender for industrial applications where once a metal housing might have been the number one choice.
Furthermore, ABS can be discoloured and degraded by ultraviolet light. This vulnerability prompted the development of Acrylonitrile Styrene Acrylate (also known as Acrylic Styrene Acrylonitrile). ASA copes better with UV light because it replaces the polybutadiene rubber found in ABS with acrylate rubber, which is more UV resistant.
ASA retains many of ABS’s desirable properties (toughness, durability and ease of manufacturing) while adding UV stability. It also withstands heat, rain and temperature fluctuations better.
Enclosures such as PROTEC are moulded from an ASA+PC blend that is strong and resistant to UV rays. ASA typically has an impact strength of 160 to 400 j/m so adding PC (850 j/m) significantly increases the durability of the material. ASA+PC is sometimes described as ASA+PC-FR due to its flammability resistance: UL 94 V-0, compared with UL 94 HB for other plastics. Flammability ratings are based on tests including ignition times, burn rates, whether burning particles are emitted, and whether the burning material self-extinguishes.
Industrial electronic enclosures must be able to withstand heavier impacts. Protection against impact is measured using IK ratings (EN/IEC 62262). These ratings originally ranged from IK00 (no protection) to IK10 (protection against 20 joules of impact energy, equivalent to a 5 kg mass dropped from a height of 400 mm). In 2021, an additional rating — IK11 — was introduced. This equates to a 10 kg mass being dropped from 500 mm, providing protection against 50 joules of impact energy. SOLID-BOX enclosures are rated IK08, meaning they can withstand five joules of impact, equivalent to a 1.7 kg mass being dropped from 300 mm.
Ingress protection is also a vital consideration, as defined by IP ratings under EN/IEC 60529. This ratings system comprises two digits: the first shows the level of protection against solid bodies and dust; the second indicates water resistance. IP 6X enclosures are completely dustproof. IP 65 housings are dustproof and offer protection against water jets. (The test is 12.5 litres/minute, 30 kPa pressure at a distance of three metres for 15 minutes.) Ratings of IP 54 and IP 65 are common for commercial and light industrial applications. More demanding environments require ratings such as IP 66 (temporary protection against flooding) or IP 67 (immersion in water 150 mm to 1,000 mm deep for up to 30 minutes). Importantly, a higher number is not always better, merely different.
And how will you power your device? Will it be connected to the mains? If so, the enclosure will need space for a cable grommet and a strain relief clamp. Hermetically sealed enclosures due to be used in areas with temperature/pressure fluctuations may need a cable gland with an integrated pressure compensation element.
Power for handheld, portable and wearable enclosures is usually supplied by a battery. Does your preferred standard enclosure cater for different cell types? Will the cell(s) be mounted on the PCB or in a battery holder/compartment? Will the battery compartment lid need a screw fitting? (This is a safety requirement for applications such as children’s toys, where cells could be a choking hazard.) Will you need a desktop or wall-mounted docking station for recharging and data transfer? Is inductive charging a requirement?
These questions lead to another important consideration: how will your enclosure be assembled? Will it need to be opened regularly for inspection and maintenance? Torx assembly screws allow access but deter tampering; they are a key requirement for medical electronics. Screwless snap-together assembly also discourages tampering (and speeds up assembly times). It enhances the aesthetics too, as exemplified by SMART-PANEL, a wall-mounted touch screen enclosure for building control technology. The housing can be reopened with a set of special tools.
Think too about any accessories you may need, including the aforementioned docking stations, battery compartments/holders, cable glands and strain-relief clamps. Handheld and wearable housings may need straps, lanyards, belt/pocket clips, key rings and eyelets. A portable instrument enclosure may require a tilt/swivel carry handle that doubles as a stand. Desktop models could require anti-slide case feet or a tilt foot bar. Wall-mountable housings will need suspension elements. Other accessories include fastening elements for DIN rails, holding clamps for tubes, and conductive seals for EMC protection.
Customisation is a requirement for most standard enclosures, usually machining of apertures for controls and interfaces, and printing of legends and logos. The latest advanced technology and smart designs make it quick and easy to transform an off-the-shelf model into a unique enclosure that can go straight to a production line for installation of the electronics.
Ideally, partner with a single-source supplier that does all the customisation work in-house. This ensures quality and accountability, and also saves time and money. Consult the enclosure manufacturer as early as possible in the design process, preferably before component layout has been finalised. This can help you to specify a smaller enclosure than perhaps was initially envisaged — enhancing device appeal and reducing manufacturing costs. It can also help you to identify design opportunities not previously considered.
For more information, view the OKW website: https://www.okw.com.au.
Mouser Electronics: Powering Innovation for Australian Engineers
Mouser Electronics offers cutting-edge components and resources to fuel the next generation of...
Thermal Profiling: Optimising Soldering Operations
Soldering operations play an important role in PCB assembly.
An intro to the software-defined car
Hardware architectures for the software-defined vehicle of tomorrow.