Hawker Richardson provides seamless implementation of SMT line at Philips Dynalite
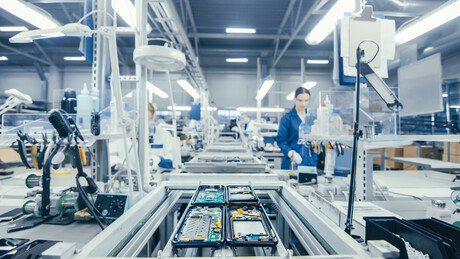
Philips Dynalite, a company of Signify, is a solution provider for lighting control systems and services, which integrate seamlessly into a smart building eco-system. Philips Dynalite’s recipe for success has always been a strong blend of good quality and highly customisable control components, and aesthetically pleasing user interfaces.
The team of experienced engineers at Philips Dynalite has recently made the strategic decision to bring their SMT operations back in-house by investing in a full SMT line supplied by Hawker Richardson. The decision to implement the line as part of their in-house production capabilities will enable the team to optimise efficiencies and productivity, as well as minimise waste and ensure every board is produced to the highest quality.
Mark Edwards, Manufacturing Manager, and Ratko Milosavljevic, Executive Director, explain how installing the SMT line is an important step and how this not only helps them improve the flexibility of production by providing the ability to set batch sizes and balance resources but how it also enables Philips Dynalite to operate with a more agile approach to customer demand.
Ratko – Can you tell us a bit about Philips Dynalite?
Philips Dynalite, a company of Signify, is a solution provider for lighting controls systems and services, which integrate seamlessly into a smart building eco-system. Many developers today aim to create buildings that are sustainable, safe, cost-effective, and human-centric. With the use of our solutions (which controls the lighting and talks to third-party building systems such as HVAC, AV, BMS and more) our customers can satisfy these goals and create an environment that responds dynamically to the changing needs of users.
Our recipe for success for Dynalite solutions has always been a strong blend of high-quality, aesthetically pleasing and highly customisable user interfaces and powerful front and back-end software solutions, connected to a robust and cost-competitive range of controllers as a backbone. Our system can be designed to meet the most demanding requirements of our customers, with almost endless opportunities to dynamically configure the system.
Ratko – Do you believe the new SMT line will drive marginal gains and improve Philips Dynalite’s profitability?
Our new SMT line brings significant efficiency and productivity improvements in many operational steps, through its seamless end-to-end integrated automation, data exchange and real-time analytics. The new line enables more advanced predictive maintenance, further supply chain digitalisation and improved quality control, leading to reduced downtime and increased efficiency through more optimised human and machine resource utilisation and waste reduction.
Ratko – Philips Dynalite is the global leader in connected lighting control. To stay competitive with technology changing by the second, do you feel pulling the electronics PCB assembly production capability back in-house enables you to maximise your dynamic capabilities to stay agile and one step ahead?
Yes. One of the key reasons for making this strategic investment in our new PCB line was to significantly improve the agility of our business in responding much faster to our customer needs with competitive, environmentally sustainable solutions, built on the latest technology.
Mark – Dynalite has a broad portfolio of lighting control components suitable for projects of almost any size or application. How important is it to now have improved flexibility in your production capabilities?
The new SMT line enables us to stock parts at the component level rather than WIP and Finished Goods. This brings our total stock holding value down but more importantly we are able to react within short lead times to customer demand. Having a range of common components between our portfolio means we are not tying up in-demand parts for slower moving assemblies. Furthermore, the ability to set our own batch sizes off the SMT line and better balance our resources enables a smoother workflow within the factory.
Mark – How important is it for Dynalite to know that they can rely on suppliers like Hawker Richardson so the focus can remain on innovation and not on machine reliability?
We were confident in partnering with Hawker Richardson and Yamaha for their industry knowledge and track record for innovation and being best-in-class. The team at Hawker Richardson have demonstrated extensive industry knowledge of new equipment and PCB production, making capital expenditure decisions easier for us. We’re confident that we have a solid platform to grow our business now and into the future.
Ratko – Dynalite is committed to improving its sustainability throughout its supply chain. How important is it that products such as the latest Heller MK7 Reflow Oven have lower electrical usage?
With a smart choice of advanced technology machine selection, such as the Heller MK7 Reflow Oven, we’ve been able to reduce the power usage and carbon footprint of our operations. This is in line with the strategic sustainability goals of Philips Dynalite, and our parent company, Signify. Additionally, these products lower our operational cost, improving our market competitiveness and enabling us to pass savings back to our customers.
Ratko – Part of your SMT line includes an Automated Optical Inspection (AOI) system. With quality being an important part of manufacturing your range of lighting control components, was purchasing an AOI system an easy choice to make? Were there any particular challenges you hoped the AOI would help you overcome?
Being a technology leader in lighting, we continuously innovate our products and services with the use of the newest technologies and electronic components. Technological advancements have brought the size of many components to a fraction of a millimetre and the modern circuit complexities have increased component count multi-fold. Traditional manual inspection equipment can no longer provide a sufficient inspection process. Therefore, the use of good quality AOI systems is imperative to establish total quality control.
Ratko – What motivated your decision to invest in Hawker Richardson instead of continuing to pursue outsourcing options, particularly in the context of reshoring?
The post-COVID-19 world has presented new business risks with traditional supply chain and manufacturing off-shoring models, whilst presenting new opportunities for re-shoring. Reshoring has many benefits for us, including but not limited to improved business agility in responding to product customisation requests, better raw material stock utilisation, reduction of “work in progress” capital, reduced packaging waste, and lower transport costs and carbon footprint.
Mark – How frequently do you anticipate operating your total line solution, and what level of productivity are you aiming to achieve with this set-up?
We plan to operate the total line solution on a daily basis, and we are currently moving towards this target. This was one of the important features we assessed during equipment selection and moving towards Industry 4.0 standards. Targeted productivity on SMT line is 98% with focus on 100% quality, reduced changeover time, and a single operator to run the SMT line (including AOI — using remote features).
Mark – Could you share your overall experience with Hawker Richardson’s service and support?
Implementation was seamless with few challenges on delivery (due to outside factors). We were delighted with the technical support from Hawker Richardson with readily available support whether this was on the phone, by email or physically on the premises when it was needed.
Mark – You hit the ground running at the same time we launched the Hawker Richardson Training Portal. Have you utilised it and how valuable was it?
Absolutely. For us, we started our training onsite with Hawker Richardson late last year in preparation for the new equipment to arrive. The addition of the training portal was instrumental for us to bring this knowledge back in-house and to teach our operators as much as we could before the equipment arrived.
...and Ratko?
For us it was critical to get a return on investment as quickly as possible. Having a portal ready to do our programming upfront, even before the machines arrived, has helped to expedite this, especially in the first three months of implementation. We had the products coming up much quicker than we otherwise would have without the portal. We strongly recommend the portal as a useful learning tool.
Mark – Would you recommend Hawker Richardson to anyone else based on your experience?
Absolutely, yes. We consider this a partnership rather than a traditional supplier/customer relationship. Hawker Richardson is readily available to offer advice and assistance as we ramp up our line.
Eliminate Unplanned Downtime: A Smarter Approach to Machine Diagnostics with the HYDAC HMG 4000
The HYDAC HMG 4000 portable data recorder provides a smarter, faster, and more precise approach...
Precision in Design: Specifying Large Handheld Enclosures for Industrial Electronics
When designing handheld electronics, ergonomics play a vital role; purpose-built plastic...
Mouser Electronics: Powering Innovation for Australian Engineers
Mouser Electronics offers cutting-edge components and resources to fuel the next generation of...